Ceramic Coatings have rapidly gained popularity, becoming essential for discerning vehicle owners demanding maximum protection and an enduring showroom shine. But what lies behind the mesmerizing finish? Let’s pop on our science hats and delve into the intricate science powering ceramic coatings, exploring their specialized nanostructured chemistry and microscopic dynamics.
THE CHEMISTRY OF CERAMIC COATINGS
At their core, ceramic coatings employ a sophisticated blend of inorganic compounds like silicon dioxide (SiO2), titanium dioxide (TiO2), aluminium oxide (Al2O3), and zirconium dioxide (ZrO2) engineered into a nanoparticle structure measuring mere nanometers in size. This nanotechnology is pivotal to their unmatched performance.
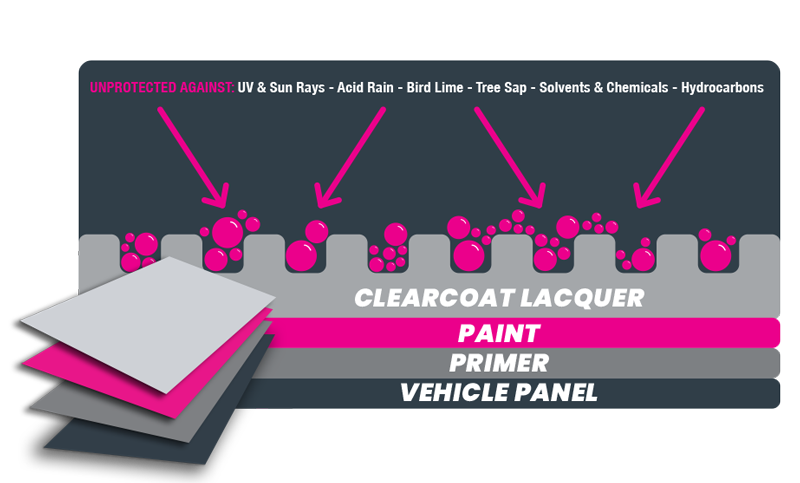
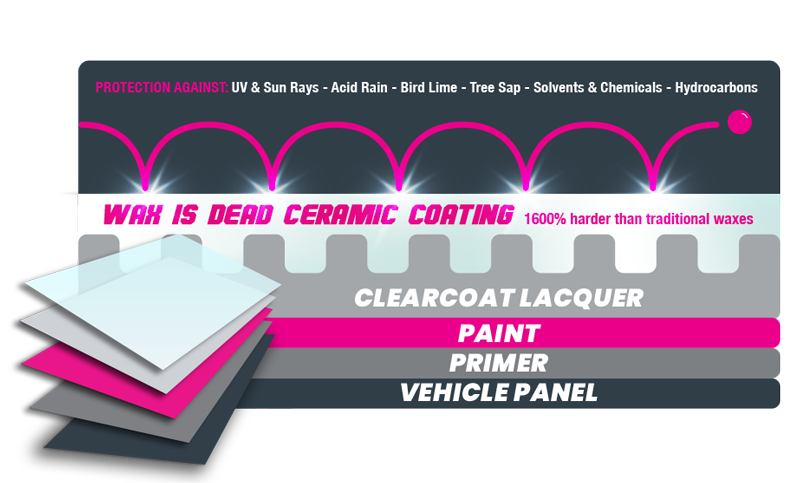
COMPOSITION AND STRUCTURE
Regular wax coatings just sit on top of a surface, but ceramic coatings actually become part of the surface itself through a chemical bonding process. Instead of just applying a coating, a ceramic coating chemically reacts to create an ultrathin but extremely durable layer that merges with the existing clear coat finish. This integrated layer gets its strength and robustness from being made up of a densely interlocked network of extremely tiny nanoparticles, both amorphous (non-crystalline) and crystalline in structure. Even though this bonded ceramic layer is less than 1/100th the thickness of a human hair, it ends up being much tougher and more permanent than a regular wax coating just sitting on the surface.
BONDING AND CROSS-LINKING
The ceramic coating bonds so strongly because of a two-step curing (hardening) process. First, the liquid coating is applied and seeps slightly into the existing clear coat surface. Chemical reactions then occur that allow the coating to form a densely interwoven network of nanoparticles. This network becomes tightly knitted and chemically bonded to the surface through very strong covalent bonds.
In the second step, either heat or UV light exposure triggers additional chemical reactions that cause further bonding and condensation within the nanoparticle network. This solidifies the structure into an extremely hard, impenetrable barrier layer unified with the underlying surface.
So, rather than just sitting on top like a wax, the two-stage curing process allows the ceramic coating to become part of the surface itself through intricate chemical bonding at the nanoscale.
HYDROPHOBIC AND OLEOPHOBIC PROPERTIES
Ceramic coatings are very good at repelling water and oils. This is because of their molecular makeup and nano-level texturing on the surface. Water and oils form nearly perfect spherical droplets on the coating instead of spreading out. This happens for two reasons – first, the intermolecular forces between the coating and the liquids are very weak, so the liquids minimally interact with the surface. Second, the surface is ultra-smooth at the nanoscale, giving the liquids very few points to grip onto and spread across. So the water and oil droplets just bead up and easily roll off the super water/oil-repelling ceramic coating
THE APPLICATION PROCESS
Achieving professional-grade ceramic coating results demands stringent preparation protocols and flawless application techniques perfected by expert detailers. For coatings like those offered by us at Wax is Dead, an approved installer network exists to ensure their products are applied to the highest standards.
SURFACE PREPARATION
Pristine decontamination using acid and alkaline treatments removes embedded contaminants like rail dust, overspray, and bonded chemical deposits that could inhibit bonding. This is followed by multi-stage machine polishing to eliminate imperfections and increase the surface area for superior adhesion.
APPLICATION METHODS
The application of a ceramic coating is a meticulous process that requires precise techniques to ensure an even, defect-free distribution of the extremely thin nanoparticle film across the entire surface being coated.
Before application, the surface must be thoroughly cleaned and polished to a mirror-smooth finish using specialized tools and compounds. This ensures the surface is free of any contaminants or imperfections that could interfere with the coating’s adhesion.
A special application pad is first saturated with a specific amount of the ceramic coating liquid. The saturated pad is then worked across each panel of the surface in overlapping sections using straight, level strokes.
Great care must be taken to apply sufficient pressure and ensure complete, uniform coverage without any bare spots, streaks, or areas of excess buildup. The coating should level out into an optically clear, seamless layer.
Throughout the application, the temperature and humidity levels in the environment must be carefully controlled and kept within strict parameters specified by the coating manufacturer. Deviations can negatively impact how the liquid coating chemically reacts and cures properly.
WAX IS DEAD APPROVED INSTALLERS
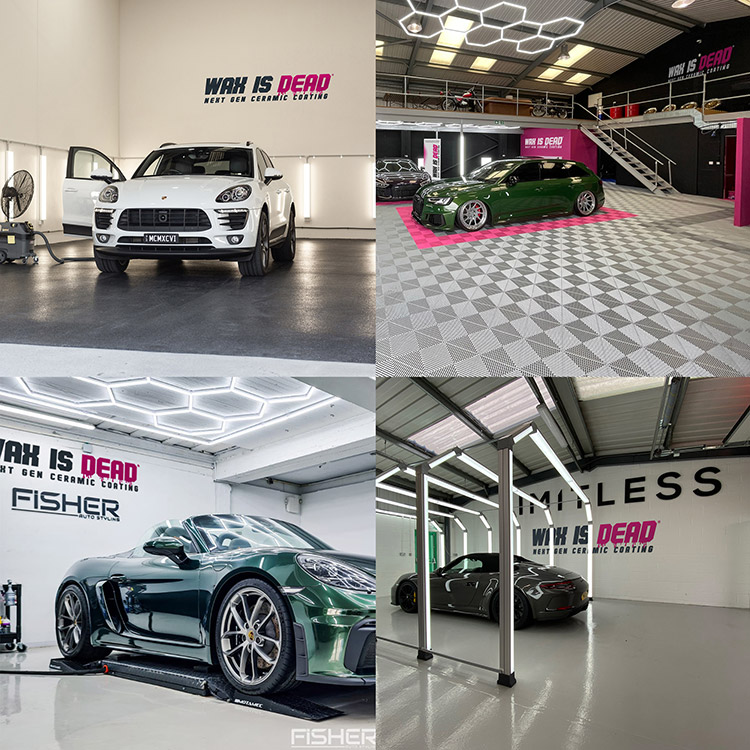
To guarantee exceptional results and preserve the coating’s warranty, Wax is Dead has established an approved installer program. Our certified professionals have shown the experience and specialized skills required for flawless ceramic coating application.
Wax is Dead-approved installers follow a stringent process, from thorough pre-application inspections to meticulous post-coating quality checks. Their experience and expertise ensure the coating bonds perfectly, cures completely and performs as designed for maximum durability and show-stopping gloss.
CURING AND AFTERCARE
Following application, the coating must fully cure over 24-72 hours, allowing for complete solvent evaporation and condensation polymerization to reach maximum cross-link density. Once cured, products like fluorinated sealants can be applied to enhance hydrophobicity. Regular maintenance cleans away contaminants that could potentially etch the coating.
By entrusting your vehicle to a Wax is Dead approved installer, you can rest assured that the ceramic coating will be applied with a level of skill that meets the manufacturer’s exacting standards. This meticulous process is vital for upholding the coating’s warranty and ensuring you experience all the spectacular benefits it has to offer.
MICROSCOPIC DYNAMICS
The true protective capabilities arise from the coating’s unique nano-engineered structure and finely tuned surface interactions.
SELF-CLEANING AND CONTAMINANT SHEDDING
The nano-level texturing on the ceramic coating surface has a very low surface energy. This means contaminants like water, oils, dirt and grime cannot spread out and stick to the surface through chemical bonding. Instead, because the coating actively repels water and oils, these contaminants form into tight, nearly spherical droplets that just bead up on the surface.
These droplets make a high contact angle exceeding 100 degrees with the coating, rather than spreading out flat. This bead-like shape prevents the contaminants from adhering or wetting the surface. As a result, the liquid beads of water, oil, dirt easily roll or rinse off the surface due to gravity or airflow, without sticking or staining. So the coated surface stays much cleaner and easier to rinse clean compared to an uncoated surface.
SCRATCH RESISTANCE
While not impervious to excessive impacts or deep gouging, the intertwined nanoparticle network structure exhibits remarkable hardness and abrasion resistance compared to polymer coatings. Its densely crosslinked matrix of ceramic oxide nanoparticles can deflect minor scratches and effectively self-heal microscopic defects through localized plastic deformation.
UV PROTECTION AND OXIDATION PREVENTION
Metal oxide nanoparticles like titanium dioxide and zinc oxide act as UV absorbers, efficiently dissipating harmful high-energy ultraviolet photons through electron transitions before they can initiate oxidation reactions. This shields the underlying clearcoat’s polymers from degradation, retarding chalking, fading, and loss of gloss over time.
ADVANTAGES AND LIMITATIONS
While offering unparalleled protective and aesthetic benefits, ceramic coatings possess both merits and limitations to evaluate.
ADVANTAGES
- Exceptionally glossy, liquid-like finish from nanotextured surface
- Extreme durability from covalently-bonded nanoparticle matrix
- Hydrophobic/Oleophobic self-cleaning from low surface energy
- Nanoparticle hardness resists light scratches, swirls, etching
- UV absorption prevents oxidation, fading, and degradation
- Potential long-term cost savings by extending clearcoat lifespan
LIMITATIONS
- Higher upfront cost compared to polymer waxes/sealants
- Potentially incompatible with damaged or degraded clearcoats
- Requires stringent surface preparation and professional application
- Does not prevent heavier impacts or abrasions
CONCLUSION
The incredible gloss and protection offered by ceramic coatings results from a convergence of innovative nanomaterials and intelligent molecular engineering. From their cross-linked nanostructure to their meticulously designed surface chemistry, these coatings exemplify the cutting edge of automotive nanotechnology. However, unlocking their full potential demands pristine application by trained professionals on well-maintained surfaces.
When properly applied and cared for, ceramic coatings equip vehicle owners with years of unrivalled showroom shine while furnishing vulnerable paint with self-cleaning, swirl-resistant, UV-shielding ceramic armour.” As nanotechnology continues advancing, ceramic coatings will prove indispensable for preserving automotive investments. For those seeking the ultimate union of aesthetic brilliance, resilient protection, and materials innovation, ceramic nanocoatings stand in a class of their own.